Innovation has always been the hallmark of Vega. That’s why, even for the most standard of cylinders, there’s room for revamping. And that’s also why we are proud to welcome a new addition to the V215 series—the brand-new CD version!
The V215 Series 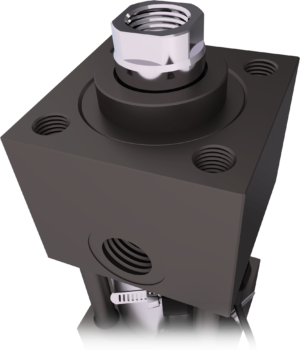
When talking about hydraulic cylinders, the most common picture that comes into mind is that of a tie-rod cylinder. Vega has been developing this sort of cylinders right from the start, designing the V215 CR series.
Produced according to the 1993 UNI EN ISO 6020/2, V215 CR are completely interchangeable with other tie-rod cylinders, even if produced by other manufacturers.
The strength of these cylinders lies in their versatility and in the number of possible fixings, which makes it easy to install them. Moreover, there are many different types of rod-ends and different diameters for each bore. Combination numbers are endless!
V215 cylinders are made of two steel heads (of different shapes, according to fixing style) connected by a tube and locking tie-rods. Inside the tube, there are the piston and the rod of the cylinder, connected together and sliding. Moreover, the rod slides through a cartridge, transmitting pushing force and movement to the mold. Of course, proper seals are implemented to prevent leaking. Guide bushes are used to avoid friction, wearing and the so-called stick-slip effect. Since the tube is non-magnetic, it’s been possible to implement a magnet inside the piston. This means that it’s possible to actuate position sensors to warn when the stroke-end position has been reached.
Even though these cylinders are not the most compact, they are probably the most versatile ones, and they are among the few compact cylinders offering long strokes. Also, they can withstand unusually high pressures, up to 215 bars. Another important feature is cushioning. When reaching the end of the stroke position, the mineral-based oil gets trapped into a special chamber, unable to flow out except through a very tiny hole, which can be regulated by the customer. Therefore, a pressure drop is generated, leading the piston to dissipate its kinetic energy and to stop very gently, without crashing. In addition to oil holes, air holes as well, when present, are quick and easy to regulate. The cylinder speed is enhanced by means of big delivery holes, bigger than most compact cylinders. That makes this type of cylinders especially useful when huge masses are to be moved (and stopped), long strokes are needed and extreme compactness is not required.
The Standard Innovation—V215 CD 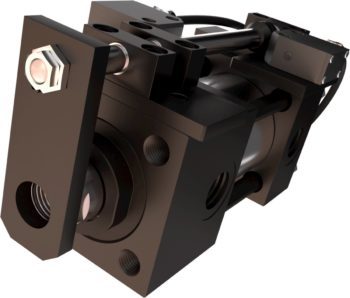
Although extremely versatile, the V215 series had one enemy—die-casting harsh conditions. That’s why the new V215 CD has been designed.
Though fewer fixing styles and rod-ends are available, and bore size starts from 50, its pros are definitely worth it.
Among the standard features of the V215 series, these additions have been made:
- Water-glycol compatible seals are now available
- It’s now possible to choose among three types of sensors—magnetic, mechanical and inductive. The latter two are very resistant, perfect for harsh foundry conditions. Moreover, a special mechanical switch is also available, overcoming the magnetic sensor limit of 80° C.
- A special version of this cylinder can be requested, offering heat-insulating plates between the cylinder itself and its sensors, so as to abate working temperatures.
What do you think of these innovations? Do you want to know more about the V215 CD series and configure your own cylinder? See the online configurator on our official website!